Sauber Motorsport optimiert das Post Processing
Sauber Motorsport setzt seit Februar für die Nachbearbeitung von SLA-Druckerzeugnissen auf seinen 3D-Systems-ProX-800-Anlagen auf eine «C1 Max» von AM Solutions – 3D post processing technology, die auch mit der neueren SLA-750-Serie kompatibel ist. Die Anlage wurde im Rahmen der bestehenden Technologiepartnerschaft der beiden Unternehmen entwickelt und punktet in vielerlei Hinsicht, insbesondere bei den wichtigen Themen Effizienz, Oberflächenqualität, Bedienerfreundlichkeit sowie Umweltverträglichkeit und Gesundheitsschutz.
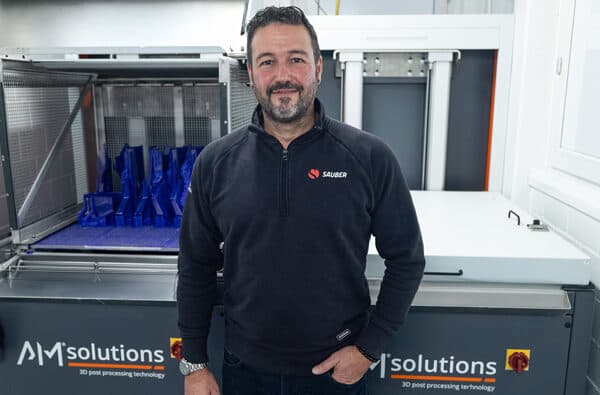
Die Bauteile, die Sauber Motorsport im SLA-Druck erzeugt, sind äusserst komplex und erfordern maximale Präzision. Dies erschliesst sich bereits aus ihrer Anwendung. So kommen sie fast ausschliesslich im Windkanal für die Formel 1 zum Einsatz und sind entscheidend für die Dynamik eines Fahrzeugs. Um hier zuverlässig und schnell qualitativ hochwertige 3D-Druckerzeugnisse zu liefern – in der Zeit von Oktober bis Februar sind es immerhin etwa 1000 Teile in der Woche –, ist eine effiziente Nachbearbeitung unerlässlich. «Wir mussten in der Vergangenheit bei der chemischen Nachbearbeitung im SLA-Bereich viele Schritte manuell ausführen», erklärt Vitor Sousa, Head of AM Plastic & CNC for AM bei Sauber Motorsport, «dies hat bei einer Anzahl von sieben Druckern nicht nur viel Zeit in Anspruch genommen, sondern war auch für die Mitarbeitenden, die mit den Lösungsmitteln arbeiten mussten, eine grosse Belastung. Seit Februar haben wir nun zwei C1 Max von AM Solutions im Einsatz und sind äusserst zufrieden.»
50 Prozent Zeitersparnis
Die C1 Max basiert auf dem Konzept der C1 und wurde von AM Solutions – 3D post processing technology speziell auf die Bedürfnisse von Sauber Motorsport hinsichtlich der Nutzung grosser Bauplattformen angepasst. Die SLA-Druckerzeugnisse werden über eine automatisch absenkbare Bauplatte in das Behandlungsbecken getaucht und von einem speziell temperierten Verfahrensmittel umspült. Ein Propeller sorgt dabei in Kombination mit mehreren, aber auch einzeln ansteuerbaren Düsen, für eine ideale Umströmung und maximale Flexibilität. Ein Gitterkorb sorgt ausserdem dafür, dass keine Teile im Tauchbecken verloren gehen oder beschädigt werden. Ein perfekt aufeinander abgestimmtes Zusammenspiel chemischer, thermischer und mechanischer Prozesse sorgt dafür, dass die Stützstrukturen aufgeweicht werden und anschliessend einfach und schonend entfernt werden können. Früher musste jedes einzelne Bauteil aufwendig von Hand mit einem Spachtel unter Einsatz erweiterter PSA-Ausrüstung bearbeitet werden. «Wir sparen uns dadurch viel Zeit. Früher haben wir für die Nachbearbeitung der Erzeugnisse unserer sieben Maschinen einen ganzen Tag benötigt. Heute reicht ein halber», erklärt Sousa. «Auch der Ausschuss wird auf ein Minimum reduziert, die Oberflächen sind von deutlich höherer Qualität und erfordern einen wesentlich geringeren Aufwand bei der weiteren Nachbearbeitung.»
Umweltfreundlicheres Verfahrensmittel
In der C1 Max kommt ein speziell von AM Solutions – 3D post processing technology entwickeltes Verfahrensmittel zum Einsatz, das umweltfreundlicher als herkömmliche Mittel ist. Dies wirkt sich auch positiv auf die Gesundheit der Mitarbeitenden aus, die nun im Raum ohne Maske arbeiten können. «Der Gesundheitsschutz unserer Mitarbeitenden war für uns ein ganz wichtiges Argument», betont Sousa. Ein grosser Praxisvorteil ist zudem, dass beim Entleeren der Anlage kein zusätzliches Equipment nötig ist. Ist das Medium gesättigt, wird es über die integrierte Pumpe sicher abgepumpt und über einen Dienstleister entsorgt. Insgesamt wurde der Reinigungsaufwand der Anlage im Vergleich zu früher erheblich reduziert.
Zukunftsorientierte Kundenlösung
Der Entwicklungsprozess der C1 Max erstreckte sich über etwa eineinhalb Jahre. Dabei wurden immer wieder Daten und Bauteile ausgetauscht. Ein wichtiger Aspekt war auch die optimale Grösse der Anlage. Diese ermöglicht die Bearbeitung eines Bauvolumens von 750 mm (Länge) × 750 mm (Breite) × 550 mm (Höhe) und damit die Bearbeitung einer kompletten Bauplatte der 3D-Systems ProX 800 oder der SLA 750. Ein weiterer Vorteil besteht darin, dass die «nackten» Platten einfach über Nacht in die Anlage gelegt und somit gereinigt werden können. «Früher haben wir die circa 25 Platten immer freitags aufwendig mit Trockeneis gestrahlt. Den Platz und die Zeit dafür können wir nun anderweitig nutzen», erzählt Sousa. Um auch für künftige Druckerversionen gerüstet zu sein, wurde mit Adaptern gearbeitet, um die Maschine flexibel auf den Bedarf anpassen zu können. «Die Formel 1 ist die Königsklasse des Motorsports, deshalb bewegen wir uns technisch am obersten Limit. Sichere und effiziente Prozesse sind für uns entscheidend und mit der C1 Max sind wir erneut einen grossen Schritt in diese Richtung gegangen», resümiert Sousa.